The Media About Us
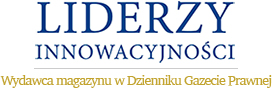
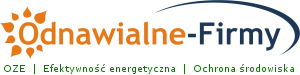
The costs of building multi-family prefabricated houses using composite-wood technology are 30 percent lower than traditional methods. The implementation time of the investment is halved, while the level of energy efficiency increases by 60 percent. Such a building is being constructed in Warsaw as part of the Smart Building program implemented by the Smart Technology Capital Group.
The design and production of prefabricated elements involve companies from the Smart Technology Capital Group specializing in composite-wood construction. Computer-controlled manufacturing allows for an unlimited possibility of creating ready-made components for building facilities according to individual design ideas and expectations.
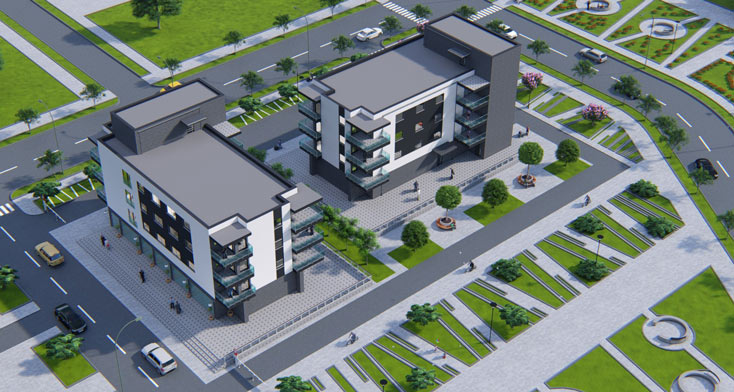
The main advantage of buildings based on composite-wood technology is the fast pace of construction. Ready-to-occupy prefabricated houses are built in just a few months. The components of the buildings: walls, ceilings, and roofs are delivered to the construction site, where they are placed on a previously prepared foundation slab within a few days. Roofing the building with tiles and other assembly works typically take another 3-4 weeks, allowing for the completion of the shell construction within a few months.
Another product offered by the Group is modular houses, which have the tremendous advantage of quick and easy construction. The entire production process involves prefabricating elements in a factory based on modular constructions. The production hall produces the structure and finishing elements, and even some of the equipment. These prepared modules are transported to the construction site, where assembly usually takes 2-3 weeks. These houses have a surface area ranging from 140 to 250 m² and are composed of several modules.
“Such solutions have many advantages,” says the person who, representing the Smart Technology Capital Group. “They accelerate construction time, which affects labor cost reduction. Additionally, work can be carried out throughout the year – regardless of the weather. Moreover, the mechanization of the production process allows for the creation of objects in accordance with applicable standards and principles of Polish construction law, ensuring a higher standard and level of quality than in traditional construction. We build energy-efficient prefabricated buildings for individual clients and also provide prefabricated construction elements for multi-family housing.”
Public utility facilities (e.g., kindergartens, schools) are also significant areas of activity for the Group. Approximately 96 percent of sales are made to foreign customers, mainly from Germany, Austria, and the Benelux countries. Due to the dynamic development, the Smart Technology Capital Group plans to enter new markets, such as Norway, the Emirates, Egypt, and Poland.
The first multi-family prefabricated building in Poland made using composite-wood technology will be available for viewing during an international conference titled “Smart Building – the future of construction”, to which the organizers invite on April 19 at 10:00 a.m. to the construction site.
Participation in the conference has been announced by, among others, the Ambassador of the United Arab Emirates to Poland H.E. Yousif Eisa Bin Hassan Al. Sabri, the Ambassador of Iran to Poland H.E. Samada Ali Lakizadeh, representatives of the Algerian embassy, authorities of Egypt, the Ministry of Infrastructure and Development, the Polish Development Fund (PFR), the National Centre for Research and Development (NCBR), and others. Event partners include, among others, State Forests, Medlabs, T-Mobile, and the Environmental Protection Bank.